
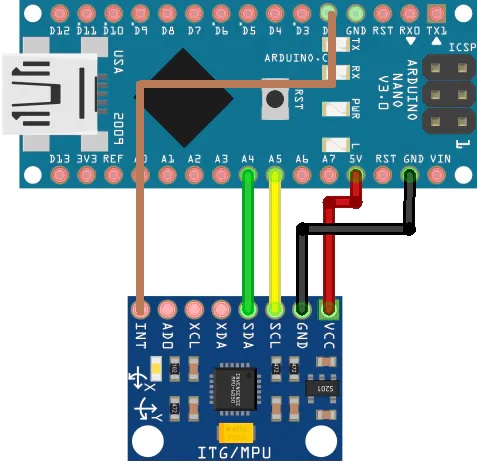
Here the input variable or set point is r(t), output variable is y(t), controlled variable is u(t) and the error is e(t). The derivative controller can deal with such because it has been looking at the rate of change of the error from the beginning. The proportional and integral controllers will respond to the magnitude of the error, but it will have a hard time catching up to how fast the error occurred. Let’s say the temperature in the furnace goes from 130 ☌ to 140 ☌ against a 120 ☌ set point in 2 seconds. This type of controller works best with dynamic errors in which both proportional and integral controllers can’t deal with. Basically, the amount of correction will be based on how fast the error is changing. If integral control looks at the history of the error, derivative control predicts the error. The integral controller will detect this, and will turn the fuel valve to its original position.įinally, Derivative control deals with the rate of change of the error. Using our previous example, an offset may be present when the fuel valve didn’t return to its original position when it increased then decreased its fuel output. Without integral control, the system can’t deal with trends on errors. Such controller produces an adjustment that is based on the accumulated error over time. The Integral controller has the ability to remove this offset and bring back the error to zero. Proportional control produces offset in its correction due to disturbances. If the error is large, the valve must release more fuel. If the error is small, the valve will release a small amount of fuel so that the set point and the feedback matches. Let’s say the controller in our example is an electronic valve for controlling the fuel to the furnace. Proportional control refers to an adjustment that is proportional to how much the error is.
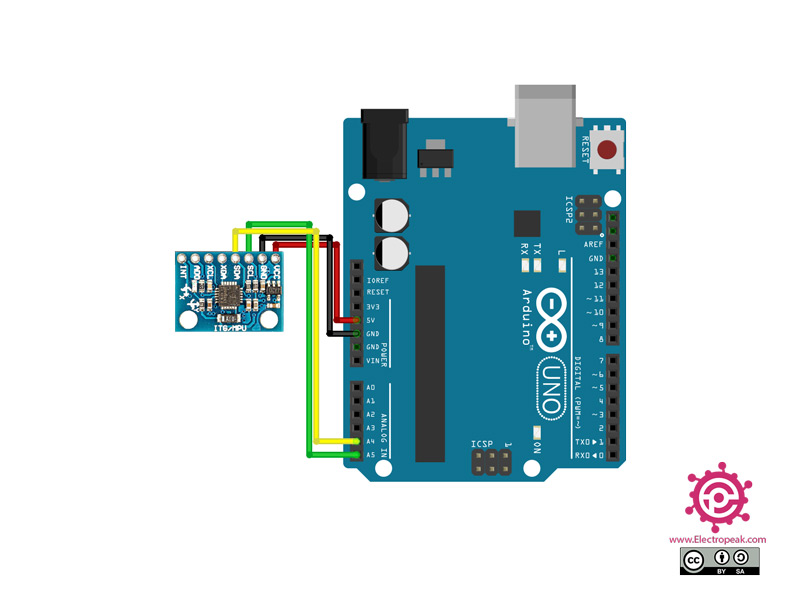
The difference between the feedback sensor value and a temperature set point is the error. This sensor, in this case, provides the feedback as a reference on the required temperature increase or decrease. A sensor installed in the furnace determines the temperature at any time. You want to maintain the temperature in the furnace to a certain set point. For example, you could have a project that controls the fire in the furnace. I suggest reading a material specifically written for such topic, but I’ll do my best to explain it here as simple as I can.Ī feedback system is a system wherein part of the output is “fed back” to the input. However, such a controller is only in feedback systems. The name comes from the methods on how such controller deals with disturbances in the system. As mentioned, PID is short for proportional, integral and derivative.
